Blog
Achieving hoisting and rigging perfection: There’s only one chance to get things right
In the challenging world of hoisting and rigging, with its high lifts, wind potential, and the need for safe movement of materials, perfection is key. There’s only one chance to get things right. Boldt’s Technical Services team offers four tips to make sure your next hoisting and rigging project goes off without a hitch.
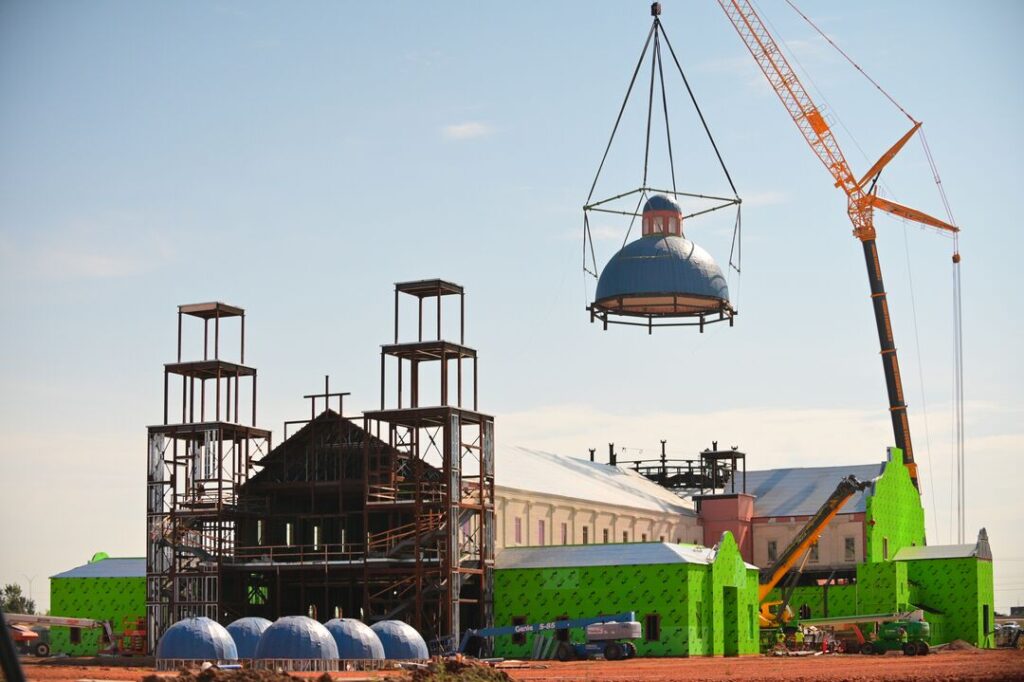
Four tips to achieve hoisting and rigging perfection
Tip #1: Plan. Plan. Plan.
Logistics: Building a tunnel in the sky
Project: Marshfield Clinic Pedestrian Connecting Bridge
Developing a hoisting and rigging plan is crucial for safe and productive lifting, keeping complex projects on schedule, and ultimately eliminating catastrophic consequences. A well-thought-out plan identifies potential hazards, provides mitigation options, builds on experience, considers environmental conditions, and stresses safety precautions.
Drawing out and sequentially mapping the H & R plan in the very early stages for the Marshfield Clinic pedestrian bridge was critical for a project that included offsite and onsite prefabrication, and the continuous lifting and moving of materials and components. Building a tunnel in the sky to support a permanent pedestrian walkway is not an easy or everyday task. The solution for the complex set of jobsite events was to prefabricate trusses in a parking lot on the hospital grounds and then lift them into place without disruption or jeopardizing hospital operations.
Just twelve weeks after construction started, crews were ready to lift the prefabricated truss sections into place with minimal impact on traffic. At 5 a.m., the self-propelled modular transport (SPMT) began to move the giant steel trusses down the road, where a 200-ton crane positioned the sections 32for crews to connect them to their foundations.
“It required tons of pre-planning to move 45 tons of steel in 10 minutes,” said Linda Danielski, senior project manager for Boldt. “We spent hours and hours in meetings between Boldt, the hospital, the city, and a nearby day care. It was amazing how all the planning paid off.”
Innovative thinking and careful pre-planning and execution of complex hoisting and rigging maneuvers minimized disruptions on the jobsite and the surrounding area and created a safer working environment.
Preplanning hoisting and lifts were key to building the “tunnel in the sky.” See how it was done.
Tip #2: Teamwork—All hands on deck
Logistics: Lifting a32.5-ton dome
Project: Blessed Stanley Rother Shrine in Oklahoma City
Problem-free lifts are the result of working collaboratively with skilled quality assurance, project management, engineering, construction, and architecture teams.
“You only get one chance. No one wants problems and it’s through good engineering that we eliminate problems,” said Marvin Rivers, director of hoisting and rigging for Boldt. Rivers and his team worked collaboratively with crews on and off site to develop a safe and effective plan for the 65,000-pound, 34-foot tall, 42-inch diameter dome lift for the Blessed Stanley Rother Shrine in Oklahoma City.
It takes an experienced hoisting and rigging team to develop and implement a plan, work through the issues, and ultimately have a project come together without a hitch. “It starts with getting the dimensions and details of what is being lifted,” Rivers said. “We start developing where the lifting load attachment is going to be, the lifting weight, the rigging components, and the capacity of the crane.” As the octagon-shaped dome was built, Boldt’s crews and subcontractor teams meticulously verified the dome’s weight, height, and dimensions were as designed and matched actual field conditions.
Ultimately though, when you lift a 32.5-ton cathedral dome, “it all comes down to trigonometry,” says Marvin. With a final check of that trigonometry, a verification of all weights and measurements, and a rehearsal lift with the crane, the plans all came to a head as the dome was smoothly lifted into place, forming the perfect crown for a monumental project.
Tip #3: Understand the Environment
Logistics: 32-Tower nacelle lift
Project: Lone Tree Wind Farm in Illinois
Neither rain, nor snow, nor sleet, nor hail, nor darkness of night …. Installing wind turbines in rural environments without existing road infrastructure poses its own challenges, but when a renewable energy construction project ran into extreme wind conditions, it complicated the original hoisting plan.
Boldt’s Lone Tree Wind Farm project the summer of 2020 was notable for more than the pandemic. Wild weather—a derecho—blew across the plains and hit Illinois with a vengeance. The wind conditions were so extreme that the project team was forced to delay lifts several times. With an already tight 6-month schedule, the team couldn’t afford to miss any windows of opportunity. Hoisting and rigging plans had to be re-evaluated to factor in the new set of circumstances.
Boldt project manager Mitch Cole monitored weather conditions, including wind speeds, daily with dataloggers placed at the top of the cranes. This ability to accurately measure wind speed and transmit the data to ground crews allowed them to make real-time decisions to safely continue or postpone crane lifts.
“It was clear that we could not make lifts in the high winds,” Cole said. “Even though we were getting to the end of the project when these conditions occurred, we needed to take our time to be safe. Turbine components on the crane hook in such conditions act as one big sail.” To avoid the sustained high winds, Boldt crews worked at night when winds had died down.
After carefully reconfiguring and rehearsing the component lifts to align with wind conditions, crews hooked hundreds of feet of tag line to top tower sections, nacelles, and rotors and successfully executed all nighttime lifts safely and on schedule.
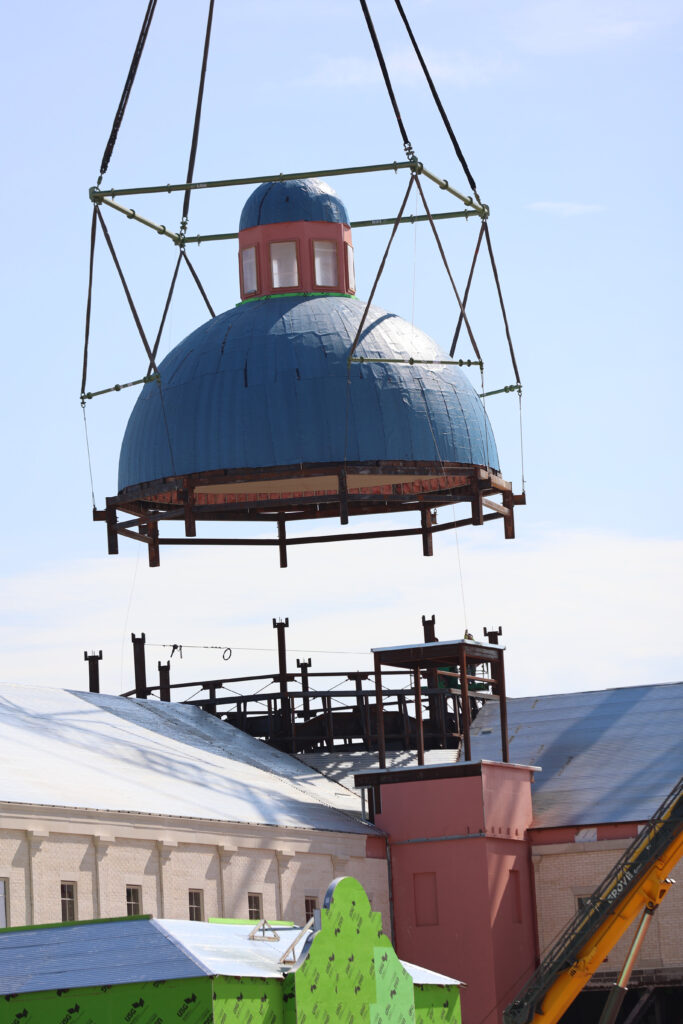
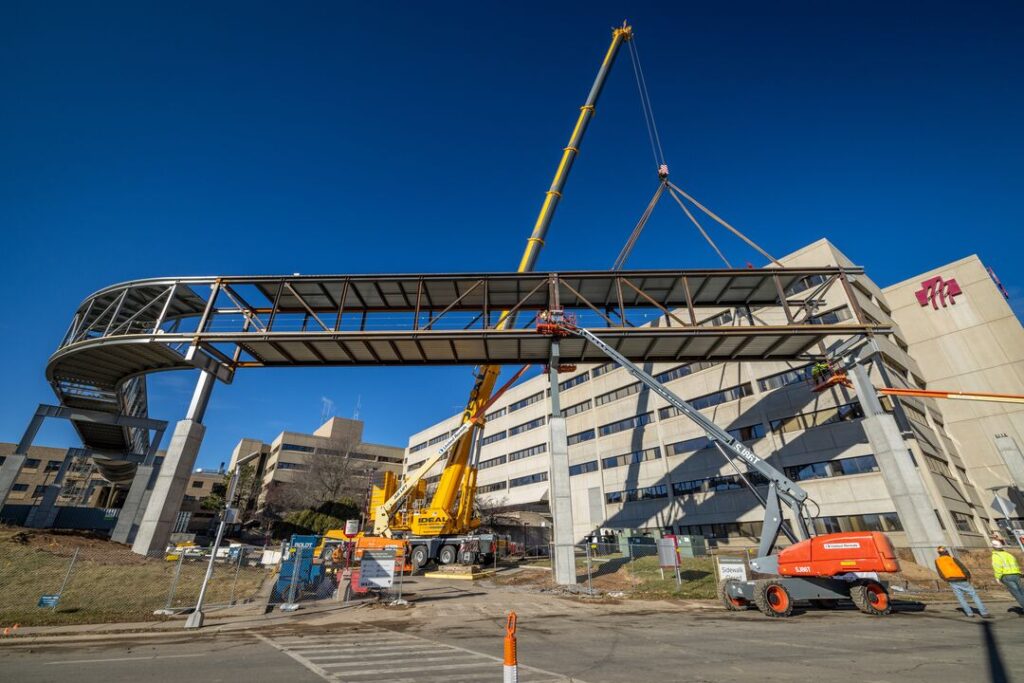
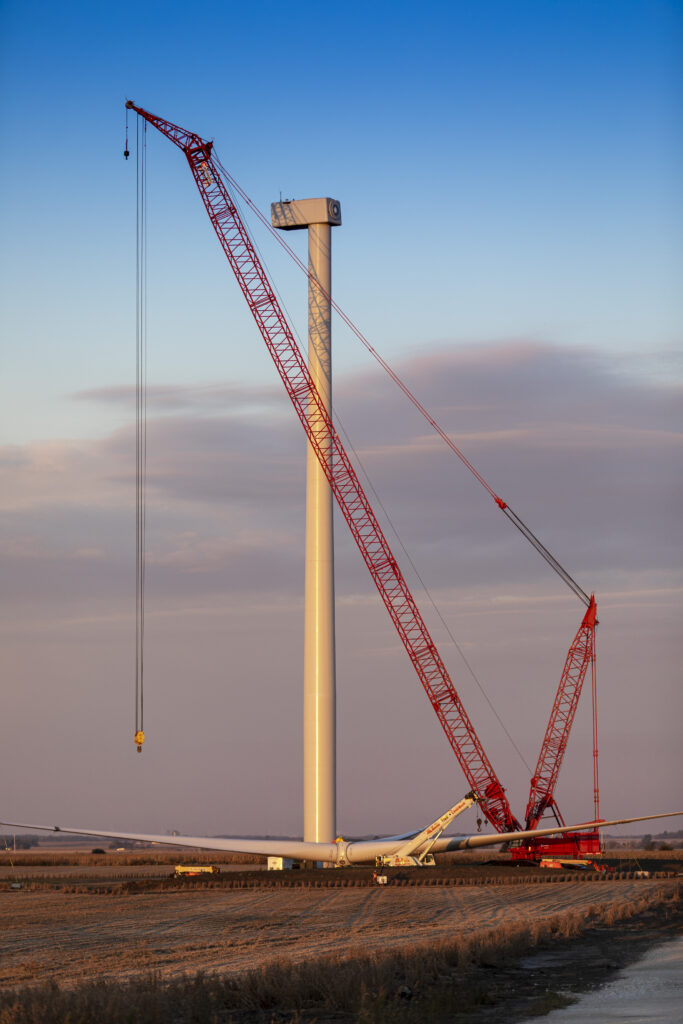
Tip #4: Experience Matters
While no two lifts are ever the same, having a partner that can build on past experiences is essential. Whether you’re building a prefabricated pedestrian tunnel in the sky, placing a copper dome on top of a shrine, or installing nacelles on wind farm turbines during rough weather conditions; experience matters.
For decades, the engineering and planning professionals within Boldt’s Technical Services (BTS) division have been perfecting the art and science of hoisting and rigging. Customization is typical in many of the more complicated projects. From equipment weight evaluation, center of gravity determination, rigging sling load determination, crane selection, ground-bearing pressure determination, lift plan layout, specialty lift frame design, and lift plan data sheets, the BTS team offers Boldt’s clients a full range of services for safe, efficient lifts of all kinds.
Offering a turnkey solution is another way that Boldt is different. Mark Davis, Boldt’s executive director of engineering and project development explains, “our ability to offer our customers a turnkey approach adds value to the construction process. We can manage and execute all stages of hoisting and lifting process, from start to finish. This makes us different than other contractors. We don’t need to outsource. We can do the lifting and lifting plans, crane selection, rigging design, and fabrication using our in-house teams. And, we aren’t intimidated when it comes to problems solving in unchartered waters.”
Want to learn more about Boldt’s Technical Services operations including hoisting and rigging?
Content Contributors:
Mitch Cole: Boldt Senior Project Manager (NPI); Lone Star Windfarm
Linda Danielski: Boldt senior project manager for Boldt; Marshfield Connector
Mark Davis: Boldt Executive Director of Engineering & Project Development
Matt Proden: Boldt Superintendent in Michigan
Marvin Rivers: Boldt Director of Hoisting and Rigging; Blessed Stanley Rother Shrine
About The Boldt Company
The Boldt Company (Boldt) is a leading professional construction services firm with customers across the United States and is a subsidiary of The Boldt Group. Founded in 1889, Boldt is a fourth-generation family and employee-owned firm headquartered in Appleton, Wisconsin. Boldt is recognized as a pioneer in Lean construction and in the industrialized construction space. Boldt operates 18 offices across the U.S. that serve customers in healthcare, power, industrial, education, automotive and commercial markets.