Blog
Growth of wind power creates opportunity and challenges
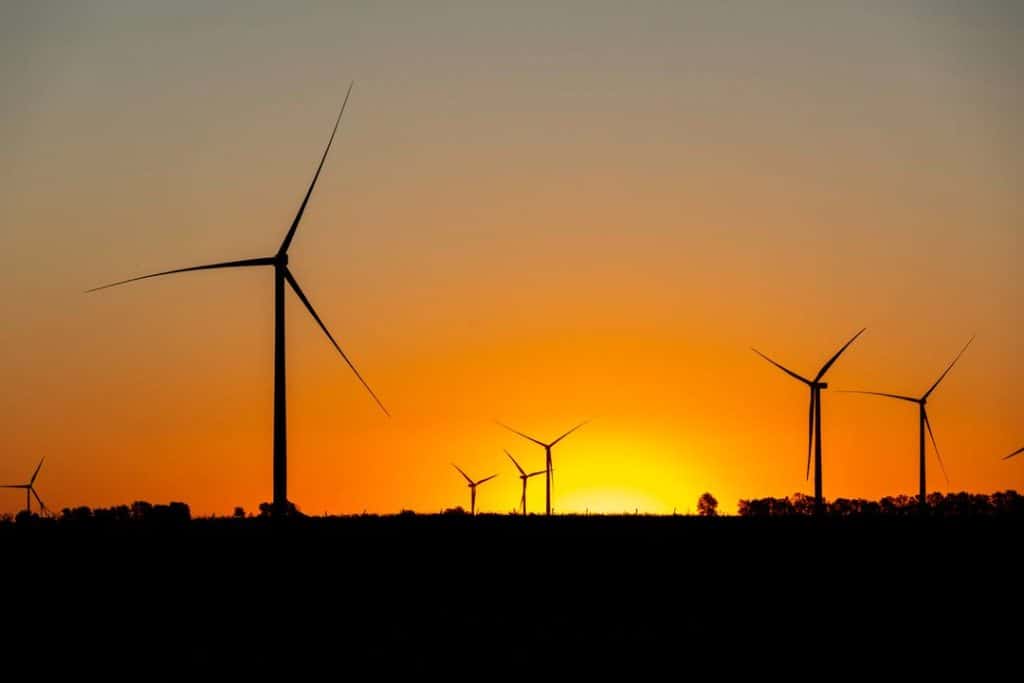
Most construction crews build on urban or suburban sites and transport equipment on existing roads, but in the world of wind farms, extreme conditions are the norm. For the Boldt Company, neither wind nor weather, nor dark of night got in the way of completing a challenging wind farm in rural Illinois.
Leeward Renewable Energy’s Lone Tree Wind Farm site consisted of soybean and corn fields spread over roughly 20 square miles. When Boldt received the order to build 32 wind turbines, it was on a site with no access roads, supporting utilities, or facilities for work. Leeward Renewable Energy was expanding its existing wind farms in Illinois and charged Boldt with assembling the team and suppliers to make it happen.
The 2.3 and 2.8 megawatt wind turbine generators were 262 to 292 feet from ground to nacelle rotor hub, and the rotor diameter of the blades was 380 to 416 feet. The turbines were anchored in foundations of about 450 cubic yards of steel-reinforced concrete. While the Boldt Company has been building wind farms since the early 2000s across the United States, this site presented a few unusual challenges.
Wild winds
The summer of 2020 was a record year for more than the pandemic. Wild weather blew across the plains and hit Illinois with a vengeance in early fall. Boldt crews planned for 20 days of weather delay in an already tight 6-month schedule and used several of them to cover high wind events on the jobsite.
Boldt project manager Mitch Cole monitored weather conditions daily with dataloggers placed at the top of the cranes to monitor wind speeds. A Bluetooth connection enabled collectors to accurately measure wind speed and transmit data to ground crews so they can make real time decisions to safely continue or postpone crane lifts.
“It was clear that we could not make lifts in the high winds,” Cole said. “Even though we were getting to the end of the project when these conditions occurred, we needed to take our time to be safe. Turbine components on the crane hook in such conditions act as one big sail.” Sustained high winds forced Boldt to work at night when winds died down.
Night work is not unusual in the power industry, but when the jobsite is in the middle of a farm field, it’s a new set of problems. Boldt’s safety team was mustered to create a plan that identified any potential problem created by working in the dark. “We had to keep the crew contained so we knew where they were, we had light plants on the tower site, the staging site, the walkways, and we had to ensure the crew had extra gear for working during colder night shifts,” Cole said.
At this late stage in construction, crews had completed 25 towers and the experience of planning and rehearsing the component lifts was already under their belts. Topout crews hooked hundreds of feet of tag line to top tower sections, nacelles, and rotors and successfully executed all nighttime lifts safely and without issue.
“From my vantage, it almost seemed easier working at night,” Cole said. “The hustle and bustle of the jobsite was reduced, and the only thing we dealt with was the task at hand. It seemed the guys were more focused on what we were doing.”
Getting there was half the problem
Before any heavy lifting started, the logistics of getting equipment and components properly delivered and staged was a major issue. The towers, hubs, and blades were delivered and assembled at the base of the tower. However, due to supplier schedule issues and to avoid demerge charges, the nacelles and generators were delivered first to a pre-designated 13-acre laydown area for staging, then to each turbine location only when ready for installation. This planning provided for a very efficient execution of the work.
“This decision almost doubled our offload speed for overall component delivery,” Cole said. “It also kept the nacelles and generators in a stable and safe area where we didn’t have to deal with them potentially sinking into a farm field.”
Boldt needed two massive Manitowoc Cranes for lifting the wind tower components plus an auxiliary crane to support each main crane. The larger cranes alone weighed over one million pounds and needed to be walked across miles of farm fields. To limit the risk of a crane tipping during construction, crews first reviewed geotechnical information to determine how much weight the ground could tolerate. This assessment resulted in use of about one-half mile of timber mats for the cranes to travel on between the 32 locations.
“When cranes ‘walk’ they exert about 3,600 pounds per square foot on the ground,” Cole said. “Had we not tested the site and reinforced the crane travel paths, we would have had a potentially dangerous situation.”
Collaboration keeps schedules on time
Leeward Renewable Energy procured all wind turbine generator components from GE Renewable Energy, and Cole credits GE’s involvement with delivering a successful project. The firm supplied components for all 32 units and contributed significantly to the successful planning and scheduling throughout the project.
“We didn’t want a cluster of trucks coming cross-country all showing up at the same time, as that makes it difficult for both parties. We made sure GE knew our exact schedule, the sites we wanted to offload at, and which components were needed, when,” Cole said.
Boldt uses a customized production system that includes elements of Integrated Lean Project Delivery ¨ which features a high degree of collaboration early in the construction pr setting schedules and building value in the process. The result is a more streamlined approach to planning, managing production schedules and budgets, and ultimately, the efficient execution of the work.ocess. In this process, construction managers, subcontractors, owners, and suppliers all participate in
The project and all 32 towers were completed on time and on budget by the November 2020 deadline.
Today’s energy landscape demands innovation, imagination and the courage to explore creative answers to the industry’s challenges. The Boldt Company has been building for the power sector for decades. We’ve seen technologies transform the industry. And we’ve kept pace.
More Resources:
Boldt’s renewable energy project profiles: http://engage.boldt.com/renewable-energy/p1
Photo gallery: https://engage.boldt.com/renewable-energy/p1/p/3
Headline Citation:
1 https://www.energy.gov/eere/wind/advantages-and-challenges-wind-energy
About The Boldt Company
The Boldt Company (Boldt) is a leading professional construction services firm with customers across the United States and is a subsidiary of The Boldt Group. Founded in 1889, Boldt is a fourth-generation family and employee-owned firm headquartered in Appleton, Wisconsin. Boldt is recognized as a pioneer in Lean construction and in the industrialized construction space. Boldt operates 18 offices across the U.S. that serve customers in healthcare, power, industrial, education, automotive and commercial markets.